DIESEL FUEL QUALITY MANAGEMENT
Diesel Fuel begins to degrade after only 22 days from the time it is refined. As such, any industry that requires diesel fuels to be stored for long periods must look towards technologies or systems that can help slow down or prevent the degradation. Diesel fuel that is maintained in a condition as close to newly refined fuel will outperform a diesel fuel that is poorly maintained. The solution is to employ corrective measures that ensure fuel stability and cleanliness (AXI International).
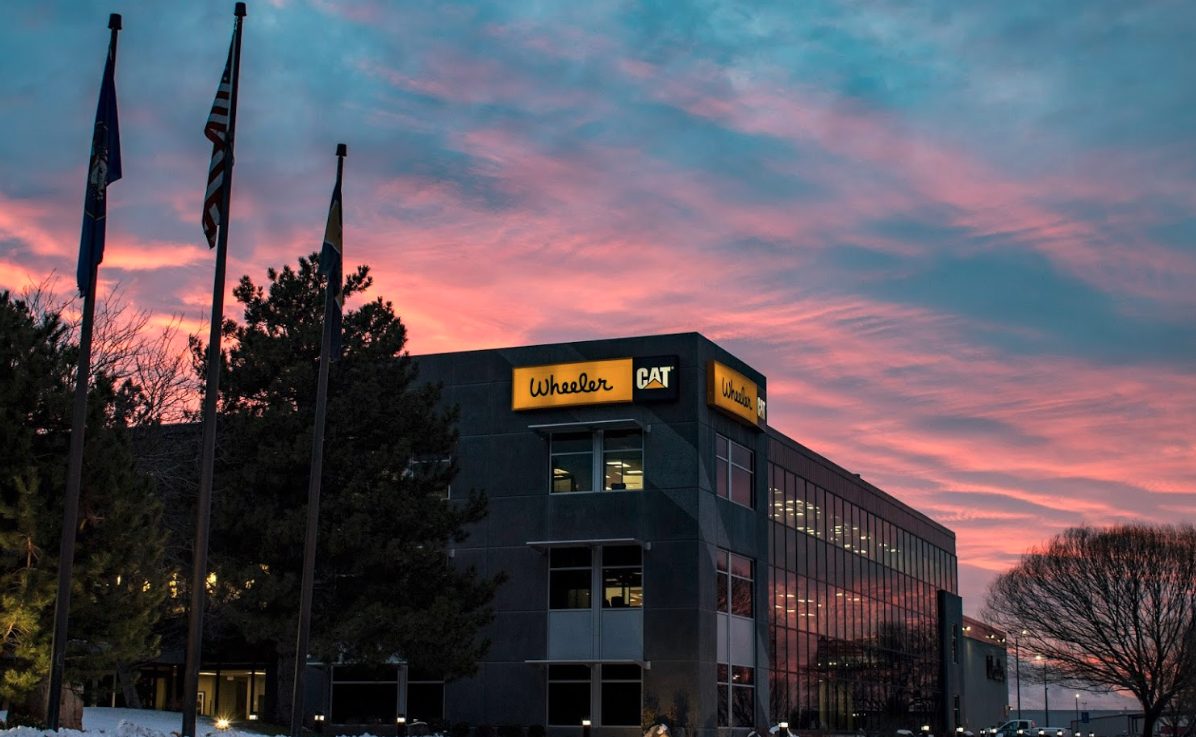
Contamination is defined as the presence of unwanted foreign substances in fluid systems or fluid wetted parts. Contamination alters the properties of fluids, causes damage of fluid systems, and prevents systems and components from attaining the desired reliability and durability. Contamination is the primary cause of fluid system failures.
– Cat Commercial Diesel Engine Fluids Recommendations
Contaminants in diesel fuel that can cause injector wear are: water droplets, particles of dust and dirt. From the terminal tank to the diesel engine tank the potential sources of contamination are (BP, U.S.):
- Dust
- Water
- Water & Dirt
RustFuel Quality Management Recommendations:
- Inspect fuel deliveries for cleanliness
- Filter the output of your fuel storage system
- Turn over fuel as frequently as possible
- Utilize desiccant breathers
A measure/treat /fuel polish strategy is the best method of protecting your diesel fuel storage tanks. Contaminants of all types can be controlled by following contamination control practices
- Maintaining a low contamination level can reduce down time and can control the maintenance cost of the machine. The productive life as well as the reliability of components and fluid systems is often increased as a result of proper contamination control practices.
- Fuels of ISO 18/16/13 cleanliness level or cleaner as dispensed into the engine or machine fuel tank should be used.
- Water in the fuel causes cavitation, corrosion of fuel system parts and provides an environment where microbial growth in the fuel can flourish.
- NFPA 110 7.9.1.3 – Tanks shall be sized so that the fuel is consumed within the storage life, or provisions shall be made to remediate fuel that is stale or contaminated or to replace stale or contaminated fuel with clean fuel.
- NFPA 110 A.7.9.1.2 – Regularly scheduled surveillance of the fuel allows the operators to evaluate the condition of the fuel. Testing should begin the day of installation and first fill.
- Severe and rapid corrosion in the vapor areas (ullage) of steel storage tanks, as well as corrosion of steel components within the tank, whether steel or fiberglass seems to be occurring with increasing frequency
A July 2016 report released by the EPA states, “The major finding from our research is that moderate or severe corrosion on metal components in UST systems storing diesel fuel in the United States could be a very common occurrence.” (Investigation of Corrosion – Influencing Factors in Underground Storage Tanks with Diesel Service)
WHAT CAUSES WATER CONDENSATION IN DIESEL FUEL TANKS?
Diesel fuel tanks are subject to water condensation because unlike gasoline, diesel fuel has no vapor pressure to displace air. When a fuel tank is warm, the air expands and is forced out. As the tank cools at night, humid air is drawn back into the tank and water condenses out on the cooler tank walls. This is one reason to keep diesel fuel tanks topped off if possible. Additional water can enter a fuel system through an open fill port, a defective tank, or when rain enters a drum that has been left open. Or it can simply be transferred from another tank that is contaminated with water.
WATER – A DIESEL ENGINE’S WORST ENEMY
PROBLEMS CAUSED BY WATER IN DIESEL FUEL SYSTEMS:
The presence of water in diesel fuel systems causes a variety of problems. Water causes steel and iron components to rust, forming loose particles of iron oxide. These rust particles can quickly clog fuel filters. Micron sized and smaller rust particles may pass though fuel filters to reach injectors, scoring surfaces and ruining fuel injection spray patterns.
Standing water at the bottom of a fuel tank provides an excellent environment for a wide variety of soil bacteria to flourish. These bacteria enter through tank openings and during dispensing. Fuel and water form an interface that provides a comfortable home where bacteria can feed on diesel fuel in a moist environment. These bacteria form a slime layer that often breaks free to rapidly clog fuel filters and disperse bacteria throughout the fuel system. A fuel filter that is plugged with bacterial slime will have a dark layer of wet gel on the upstream surface. Living bacteria pump out acids as a waste product, further corroding and damaging fuel system components.
Finally, any water that makes its way through to the fuel injectors reduces the lubrication properties of the diesel fuel along the way. This leads to galling, premature wear, damaged injection tips, and further corrosion of sensitive fuel system mechanical components.
When diesel fuel contaminated with water is pumped from a fuel tank, the water leaves the tank as visible floating droplets which are relatively easy to remove from the fuel using a quality fuel/water separator. If the water is not removed prior to passing through the pump, the diesel fuel/water mixture forms a stable emulsion making it very difficult to remove the water. Water dispersed this way may pass through the fuel system to be burned, but more likely, some will settle in, and corrode sensitive components.
Excessive diesel fuel contamination can cause premature clogging of diesel fuel filters, depending on the level of both hard and organic particles, and premature wear of modern fuel injection system parts. These impacts, depending on the size and the nature of the particles, will lead to:
- Reduced Part Life
- Part Malfunction
- Engine Failure
- Increased Exhaust Emissions
Several studies have been conducted on fuel cleanliness coming out of the pump, and it is not uncommon to find a newly-delivered batch of diesel fuel with an ISO cleanliness level of 22/21/18, which is well above the major engine manufacturers recommendation and ISO specification of 18/16/13.