INFRARED THERMOGRAPHY
The use of thermal imaging cameras has revolutionized predictive maintenance inspections for various electrical components and equipment. It can provide substantial cost savings by identifying potential electrical problems before failure thereby avoiding unscheduled downtime. As electrical equipment ages, component fatigue due to heating, increased conductor resistance, loose connections and overloading can cause equipment failures. Infrared (IR) Thermography detects thermal patterns and associated temperatures of components to identify potential issues. Once these hot spots are identified, customers can isolate energy sources to inspect and repair equipment before a failure.
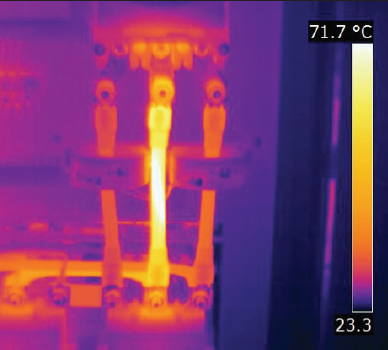
COMPONENTS THAT BENEFIT FROM IR THERMOGRAPHY TESTING:
- Utility Feeds
- Substations
- Transformers
- Switchgear
- Motor Control Centers
- Lighting Panels
- Distribution Panels
- Circuit Breakers
- HVAC Equipment
- Automatic Transfer Switch
- Battery UPS
- Fire Pump Panels
- Emergency Power Panels
FREQUENT CAUSES OF ELECTRICAL EQUIPMENT AND COMPONENT FAILURE:
- Aged equipment
- Loose connections
- Component fatigue
- Overloading
- Oxidation
- Contamination
Wheeler technicians are trained Level 2 Thermography technicians. They adhere to NFPA 70E electrical safety standards and use all appropriate PPE necessary to perform the work needed. Please call our office with any questions regarding NETA testing specifications or NFPA requirements.
For more information, please contact us.