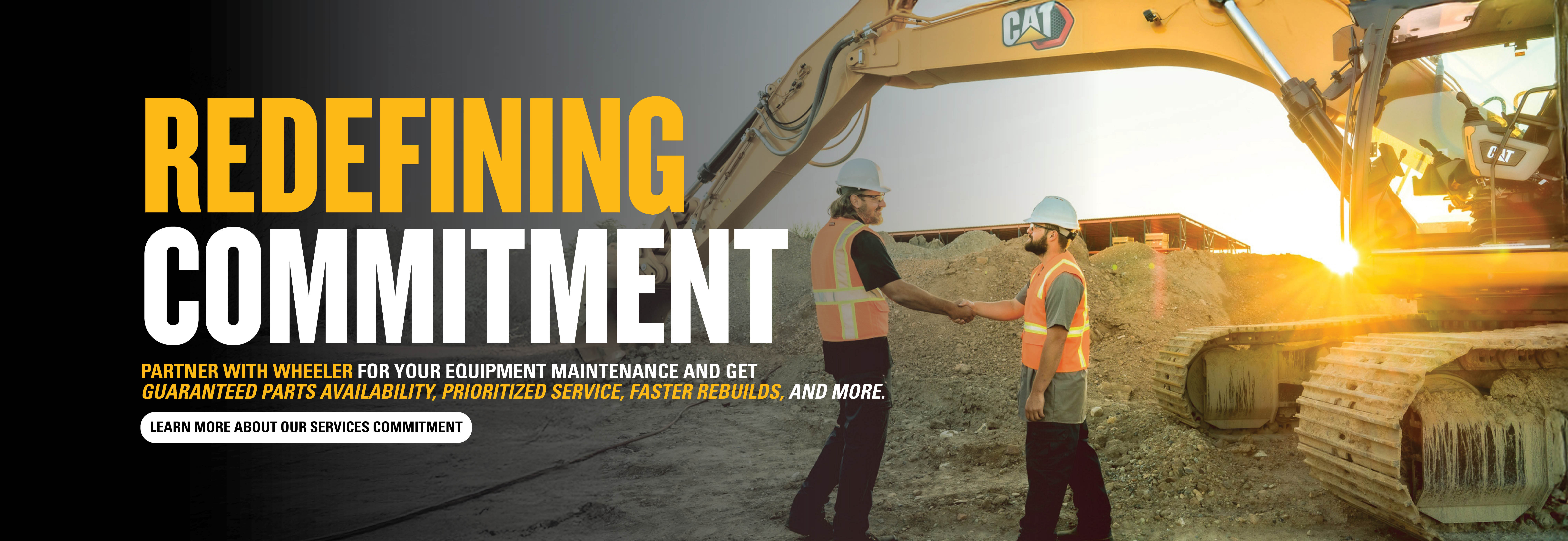
We Proudly Support The Ones Who Build Our World
Your Heavy Machinery Experts
At Wheeler Machinery Co., we sell and support Cat Equipment. We’re committed to supporting your equipment needs—your way. Whether you prefer to handle maintenance yourself, get expert guidance from our technicians, or rely on us for complete on-site service, we’ve got you covered. Our tools, resources, and expert support help you maximize uptime, reduce costs, and boost profitability—partner with us for total equipment care and success on every job.
Our locations
Dependable and Reliable
You depend on your heavy equipment every day. Depend on us for maintenance and repair.
18
Locations
73
Years in business
24
Hour machine monitoring
90
Field service trucks
3,300
Years of technician experience
15
Lube Service Vehicles
62,051
Part Numbers in Stock
400
Service Technicians
150,000
Square feet of shop space
100
Repair bays
5
Star contamination control
3,100
Rental units
Maintain your Cat Equipment With Utah’s Best
You depend on your heavy equipment every day. You can trust Wheeler Machinery Co. to help keep your excavators, bulldozers, motor graders and other essential machines on the job and performing at a high level by offering a wide assortment of maintenance and repair services. We support construction companies and other businesses throughout Utah and portions of Wyoming and Nevada.
Request Service Service OptionsLocally owned and operated
Since 1957, Wheeler Machinery Co. has been Utah’s trusted partner for Cat construction equipment and a wide array of construction tools. From excavators and bulldozers to backhoes and more, we equip your projects for success. Beyond sales, we offer flexible rental options to keep your worksite productive, whether your needs are short-term or long-term. Our team offers expert guidance, ensuring you find the perfect equipment solution. Discover reliable, well-maintained machinery and experience industry-leading support at Wheeler Machinery Co.
More About Us